Carbon Brush For Motor
Brushes are usually called carbon brushes in electric tools. It is a component of the motor. In addition to connecting the electrone and the external circuit in the motor, it also plays the role of a current. A weak and important link of the motor is formed by the brush with the directioner. There is not only mechanical wear and mechanical vibration between the brush and the directioner, but also a severe spark at the time of use, which will greatly reduce the life of the wiper, but also affect the normal operation of the motor. Therefore, the reasonable selection of brush materials, size and spring pressure, which will play a very important role in improving the directional performance of the motor and extending its service life.
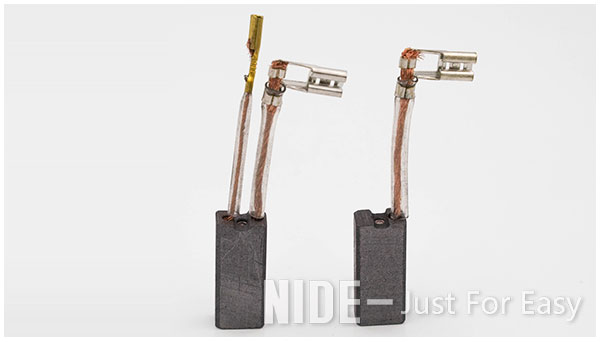
The selection of the carbon brush is mainly based on the temperature ascending of the brush, and the direction of the direction of the direction is determined. The temperature rise of the brush is related to the density of the bristle with the density of the directional contact, the mechanical loss and the thermal conductivity of the brush. If the speed of the circular line is too high, it is easy to heat the brush and the directioner, the spark increases, and the wear of the brush and the wiper is exacerbated.
From the perspective of use, there are mainly the following signs of the use of good brushes: the following situations:
1) When the brush is running, it is hot, noise, no damage, no color, not burning;
2) Have a good directional performance, inhibit the spark in the allowable range, and the energy loss is small;
3) Long service life and do not wear a wiper, do not make the wiper scratch, unevenness, burning, drawing, etc.;
4) During the operation, a uniform, moderate, and stable thin oxide film can be formed quickly on the surface of the directioner.
The structure of the carbon brush
The installation direction of the brush of the graphite brush is: radial type, back tilt and front -tilt. In the commonly used radial structure, the pressure of the spring is also different. There are mainly nest line springs, spiral springs, and stretch spring. These three spring pressing methods are to directly act on the brush by the pressure of the spring.
Classification and performance of brush
1. Classification
Brushes are generally classified according to their embryo material composition and process treatment methods
a. Carbon graphite brush type
Natural graphite brush: such brushes have a high contact voltage, good rectification performance, low -flow performance is lower than the electrical graphite brush, good lubrication performance, and used for high lines with high line speeds It
Resin bonding graphite brush: This type of brush is characterized by large resistance, reduced contact voltage, good conversion performance, antioxidant, and abrasion resistance is ideal, but the power consumption is mostly used to AC streaming motors.
b. Electrifying graphite brush
Graphite -based brush (soft brush): It is characterized by low friction coefficients, good lubrication performance, good setting performance, thermal stability, and antioxidant performance; large synchronous motors with higher line speeds and instant impact loads Large rolling motors, and small and medium -sized DC motors;
Coke base brush (medium hard brush): It is characterized by a large contact voltage drop, has a good ability to form a film, has a good ability to replace the direction, has a certain flow of rolling motors with a certain impact load, etc. And general DC motors with voltage higher than 220V;
Carbon ink brush (hard brush): This type of brush belongs to high -resistance brush for electro -chemical graphite brush. It is characterized by a large brush contact resistance and good directional performance. It is used for DC motors with difficulty in changing direction.
c. Metal graphite brush class
It consists of metal and graphite. The characteristics of the metal and graphite are adjusted by the characteristics of good metal conductivity and good lubricating lubrication. It is characterized by small contact voltage, resistance coefficient and electricity loss. This brush is mainly used for low -voltage large current motors and low -voltage AC winding motors.
Natural graphite brush and electroextburra brush resistor coefficients and brush pressure drops are large, more abrasion resistant, and the line speeds are allowed to be used (can reach 50 ~ 70m/s). Metal graphite brush resistor coefficient and brush voltage decreases less, and the abrasion resistance is poor. The line speed allowed to use is low. About 15 ~ 35m/s.
The main items of the brush technology include resistors, hardness, hardness on a pair of brushes, friction coefficients, 50H wear, etc. The resistance coefficient is a physical quantity to measure the conductive performance. At 230V, the electrical brush resistor coefficient can be selected larger, and the 120V brush resistor coefficient must be smaller. Electric 120V motor currents with the same power is larger than 230V. Heating, the grip temperature may be super worse.
The contact voltage drop of a pair of brushes is the difference in the potential difference between the current flowing into the brush through the switch to the brush. When the brush is in contact with each other, and the resistance of the contact surface when the contact surface occurs under the action of external forces, it is called friction. The ratio of friction and spring pressure is the friction coefficient of the brush and the directioner. 50H wear value: Under the specified experimental conditions, the brush is determined by the current density and the prescribed unit pressure. When the transitional line speed is 15m/s, the amount of wear of the brush is grinded by 50h.