Carbon brushes are a crucial component in the operation of various industrial machines, particularly those that rely on electric motors. These small but essential parts conduct electrical current between stationary wires and the rotating parts of the motor, enabling smooth and efficient operation. However, like any mechanical component, carbon brushes require regular maintenance to ensure optimal performance and longevity. In this article, we will discuss the importance of carbon brush maintenance for industrial equipment, outline key maintenance practices, and highlight the potential consequences of neglecting this critical task. As a leading provider of industrial solutions, "Nide International" is committed to helping businesses maintain the reliability and efficiency of their equipment through proper carbon brush care.
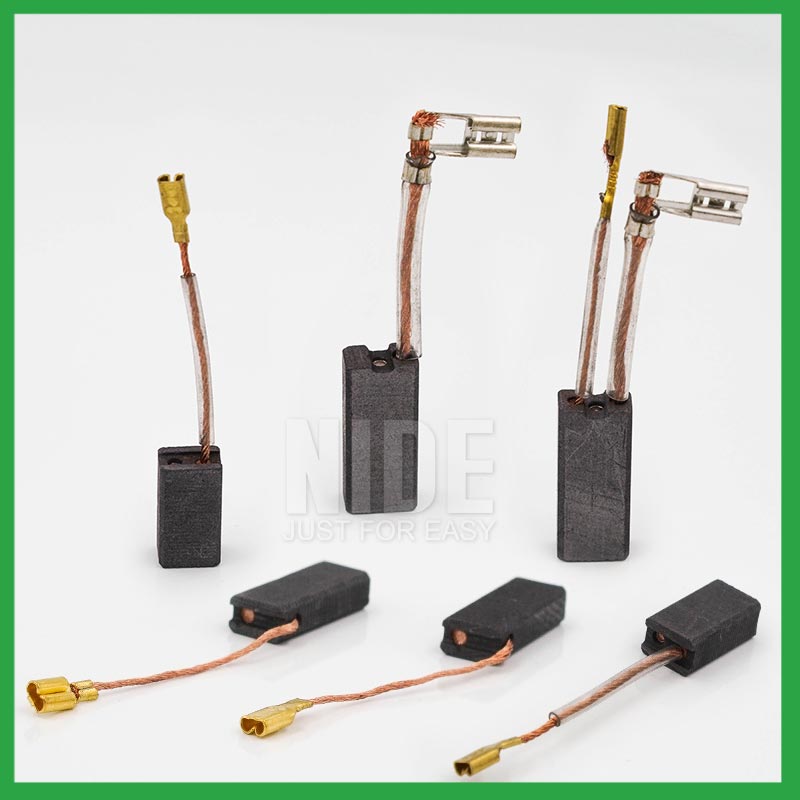
The Importance of Carbon Brush Maintenance
Carbon brushes are subjected to constant friction and electrical wear during operation, which leads to gradual deterioration. Without proper maintenance, worn or damaged brushes can cause a range of issues, from reduced motor efficiency to complete equipment failure. Regular maintenance of carbon brushes is essential to:
-
Ensure Efficient Operation
- Properly maintained carbon brushes help maintain consistent electrical contact, which is crucial for the smooth operation of the motor. Regular checks and replacements prevent interruptions in electrical flow, which can otherwise lead to fluctuations in motor performance. Studies indicate that regular maintenance can extend the lifespan of carbon brushes by up to 50%, significantly reducing the need for costly repairs or replacements.
-
Prevent Equipment Downtime
- Equipment downtime can be a costly issue for industrial operations, leading to lost productivity and revenue. By regularly inspecting and maintaining carbon brushes, businesses can prevent unexpected breakdowns and minimize downtime. This is particularly important in industries where continuous operation is critical, such as manufacturing, mining, and power generation.
-
Extend Motor Lifespan
- Worn-out carbon brushes can cause excessive wear on the commutator or slip rings, leading to more severe damage to the motor over time. Regular maintenance helps protect these components, thereby extending the overall lifespan of the motor. According to trade data, replacing a large industrial motor can cost upwards of USD 20,000, not including the additional costs of labor and lost production. Proper brush maintenance is a cost-effective way to avoid these expenses.
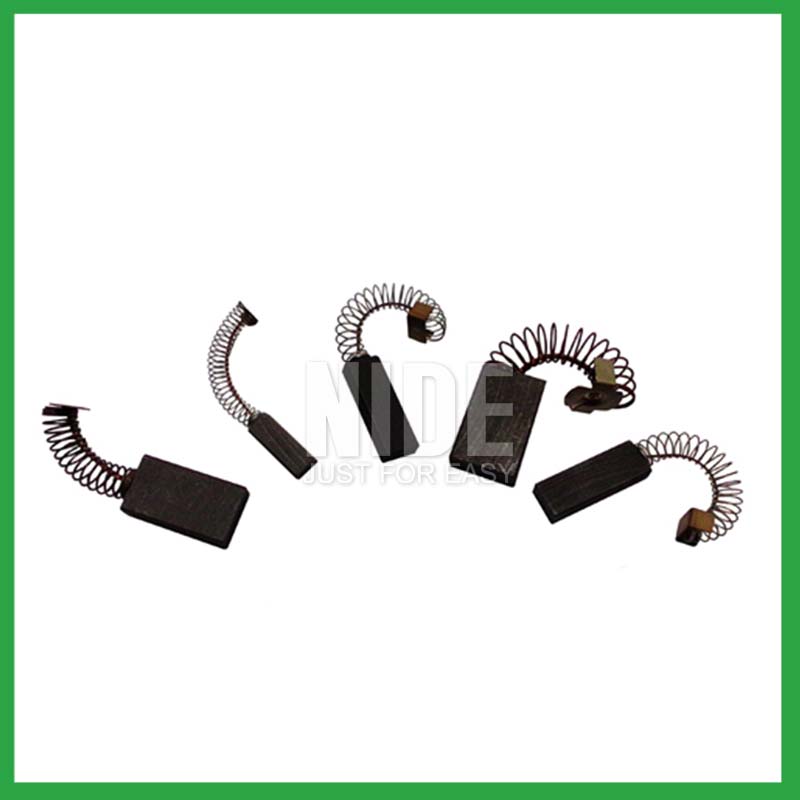
Key Maintenance Practices for Carbon Brushes
Effective carbon brush maintenance involves several key practices that should be carried out regularly to ensure optimal performance:
-
Regular Inspection
- Carbon brushes should be inspected regularly for signs of wear, such as reduced length, chipping, or uneven wear patterns. Most manufacturers recommend inspecting brushes every 500 to 1,000 hours of operation, depending on the specific application and operating conditions. Nide International suggests maintaining a log of inspection dates and findings to track wear patterns over time.
-
Brush Replacement
- Carbon brushes have a finite lifespan and must be replaced once they reach a certain level of wear, typically when they are reduced to about 25% of their original length. Failing to replace worn brushes can result in poor contact with the commutator or slip rings, leading to arcing, increased heat, and potential damage to the motor. Using high-quality brushes, like those supplied by Nide International, ensures longer intervals between replacements.
-
Commutator and Slip Ring Maintenance
- In addition to maintaining the brushes themselves, it is important to keep the commutator or slip rings clean and free of debris. Regular cleaning with a non-abrasive cloth or brush helps remove carbon dust and other contaminants that can interfere with electrical contact. In some cases, light resurfacing may be necessary to restore a smooth, conductive surface.
-
Proper Brush Seating
- When installing new carbon brushes, it is crucial to seat them properly against the commutator or slip rings. This ensures even contact and prevents excessive wear. A common method for seating brushes is to run the motor at no load or low load for a short period, allowing the brushes to conform to the shape of the commutator or slip rings.
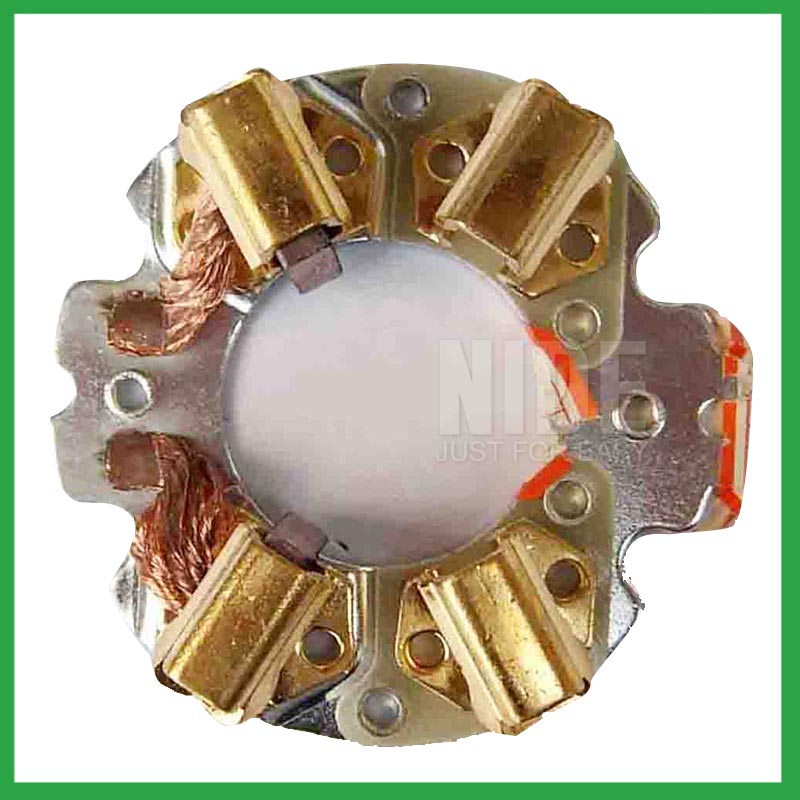
Consequences of Neglecting Carbon Brush Maintenance
Neglecting carbon brush maintenance can lead to a range of issues, including:
-
Increased Motor Wear
- Worn brushes can cause uneven wear on the commutator or slip rings, leading to costly repairs and reduced motor efficiency.
-
Electrical Arcing
- Poor brush contact can result in electrical arcing, which generates excessive heat and can damage both the brushes and the motor.
-
Reduced Motor Efficiency
- As brushes wear down, they can cause increased resistance and reduced efficiency, leading to higher energy consumption and operational costs.
Conclusion
Proper carbon brush maintenance is essential for ensuring the efficient and reliable operation of industrial equipment. By regularly inspecting, replacing, and maintaining carbon brushes, businesses can prevent costly breakdowns, extend the lifespan of their motors, and maintain optimal performance. Nide International is dedicated to providing high-quality carbon brushes and expert guidance to help businesses keep their equipment running smoothly. Investing in regular maintenance is a small cost compared to the significant benefits of avoiding unexpected downtime and extending the life of your industrial machinery.
Product: Long life and low noise motor carbon brush