PRODUCTS
CONTACT US
Ningbo Nide International Co., Ltd.
一一
· Contact person:Jack Zeng
· Mob/Whatspp/WeChat:0086-13738869026
· Email:emarketing@nide-group.com;marketing4@nide-group.com
· Add:No. 169, Wohushan Road, Daqi Subdistrict, Beilun District, Ningbo, China
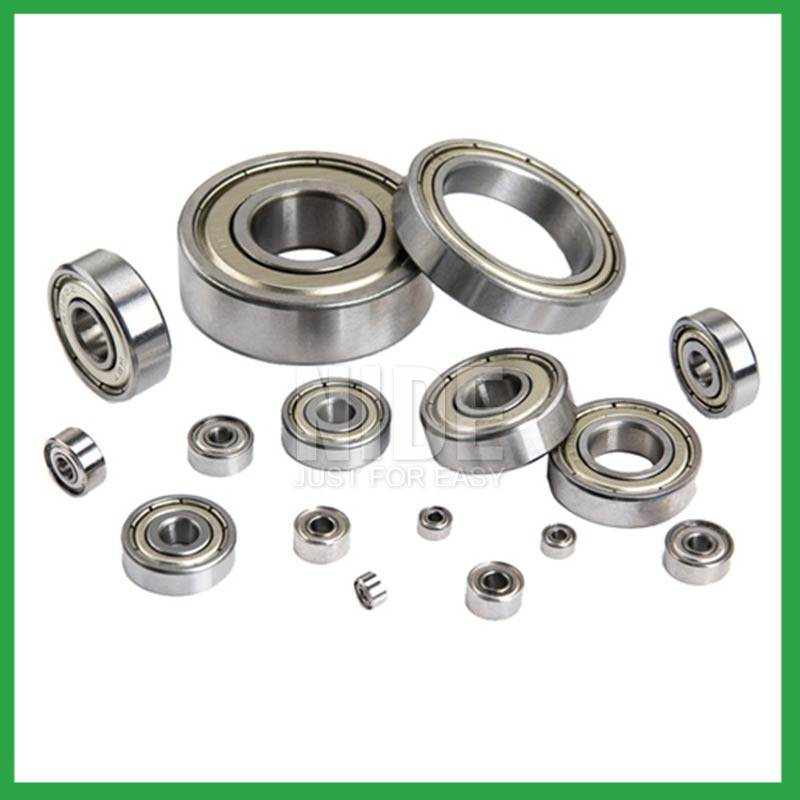
Nide team could manufacture ball bearing as per customer’s drawing and samples.
If customer only has samples, we could also design drawing fo r our customer.
We also provide customized service.
Our ball bearing is widely applied the different industrials.
Established in 2010, Ningbo Haishu Nide International is a company devoted in the field of electric motors manufacturing, providing one-stop service for its customers. Nide has three main business divisions. The first division is to provide different kinds of motor manufacturing machinery, including stand along machine, fully-auto complete line for armature and stator production, and the motor assembly line. The second division is to supply the full range of commutator,thermal protector,ball bearing,carbon brush,fan,magnet,etc. The third division is to provide technical support and consulting, project support and turn-key service for some motor manufacturing.
Parameter | Information |
Product Name | ball bearing electric motor |
Place of Origin | China |
Brand Name | Nide |
Material | ceramics, etc. |
Type | Ball |
Warranty | 3months-1year |
Port | Ningbo/Shanghai |
Application | various industrial equipment, etc. |
Size(mm) | customize |
Color | Silver gray+customized |
Precision Rating | as per customer's requirement |
Certification | ISO 9001 Certification,CE-stator coil winding machine,ISO9001:2015 certificate,etc |
Feature | High precision,Strong carrying capacity...etc |
Packaging Details | Suitable for sea transportation |
Service | one-stop service |
Model Number | ball bearing |
Supply Ability | 100000-500000 Piece/Pieces per Month |
Lead time (days) | 15-20 (To be negotiated) |
Please note: The above table data is for reference only. For specific information, please contact us.
ball bearing electric motor can be used in household appliances, such as barrel machine spindle bearings,mixers,washing machines,upper and lower pressure rods, etc; It can also be used in industrial fields, such as motors,dishwashers,weighing machines,weaving machine spindle bearings, etc.
During the disassembly process, the outer shell should be kept intact to avoid unnecessary damage;
When replacing installation components, attention should be paid to the accuracy of the support components to prevent deformation;
During the disassembly process, attention should be paid to protecting the surface quality of the ball bearing to ensure its performance;
During the operation, attention should be paid to removing surface dust to ensure the quality of the ball bearing.
Ball bearings have many advantages, making them highly competitive in the market.
Firstly, they are very durable and have good wear performance, making their service life longer than many other types of bearings.
Secondly, they are easy to install and can provide low friction performance in various applications.
Thirdly, they require a relatively low level of maintenance, making them cost-effective.
In addition, compared to many other types of bearings, their purchase cost is relatively low, making them an economical choice.
ball bearing electric motor---FAQs Guide
2.What is the significance of ball bearing electric motor lubrication, and how does it affect bearing lifespan and performance?
3.How do ball bearing electric motor handle radial loads, axial loads, and combined loads, and what are their load-carrying capacities?
4.Can ball bearing electric motor handle shock loads and high-impact conditions in heavy machinery?
5.What is the typical noise level associated with ball bearing electric motor, and how are noise-reduction techniques applied?
6.What is the load distribution within a ball bearing electric motor, and how does it vary between different bearing configurations?
7.Do ball bearing electric motor come in various tolerance classes?
8.What is the production capacity of the factory for ball bearing electric motor?
9.Are there specific ball bearing electric motor designed for applications in the aerospace and aviation industries, and what standards do they adhere to?
10.Can ball bearing electric motor be customized with special coatings or treatments to meet specific industry standards or regulatory requirements?
11.How do manufacturers ensure the quality and reliability of ball bearing electric motor through material selection and precision machining?
12.What are the considerations for selecting sealed or shielded ball bearing electric motor to protect against contamination and retain lubrication?
13.How do preloaded ball bearing electric motor enhance rigidity and reduce clearance in high-precision applications?
14.Are there self-aligning ball bearing electric motor that accommodate misalignment and shaft deflection in rotating equipment?
15.How do different ball bearing electric motor designs, such as deep groove, angular contact, or thrust bearings, cater to specific applications?
1.About ball bearing electric motor,What about the lead time?
3-7 days for samples, 3-4 weeks for mass production.
2.What is the significance of ball bearing electric motor lubrication, and how does it affect bearing lifespan and performance?
Bearing lubrication is vital for preserving the performance and lifespan of rolling element bearings. Lubrication helps separate moving parts relative to one another, such as rollers and raceways or balls, to prevent wear and tear and friction.
3.How do ball bearing electric motor handle radial loads, axial loads, and combined loads, and what are their load-carrying capacities?
The type of bearing used also varies between these loads. While deep-groove ball bearing electric motor are better equipped to handle radial loads, thrust ball bearings are designed for axial loads. However, it's essential to note that most bearings, such as angular contact ball bearings, can handle both radial and axial loads.The Bearing Static Capacity, Co, is the maximum load that can safely be applied to a non-rotating bearing that will not cause subsequent bearing operation to be impaired. It is based on calculated contact stress at the center of the most heavily loaded rolling element where it contacts the Inner Race.
4.Can ball bearing electric motor handle shock loads and high-impact conditions in heavy machinery?
As a general rule, ball bearing electric motor are used at higher speeds and lighter loads than are roller bearings. Roller bearings perform better under shock and impact loading. Ball bearings tolerate misalignment better than roller bearings do. Roller bearings can handle heavy combined radial and thrust loads.
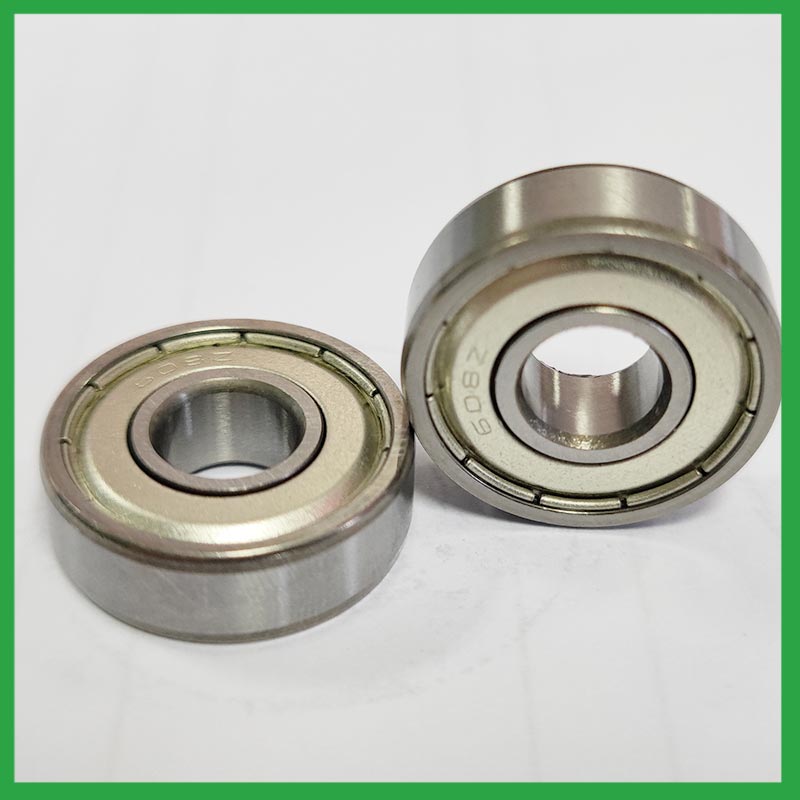
5.What is the typical noise level associated with ball bearing electric motor, and how are noise-reduction techniques applied?
To measure in accurate way the ball bearing electric motor noise under rotation during their manufacturing process is a key activity particularly in the production of medium, small and ultra-small deep groove ball bearings. This capability in bearings noise analysis has become the real distinguishing element between a standard bearings noise equipment and a superior class one.
The various types of vibration and sound in rolling bearings can be grouped in four main categories: structural, manufacturing, handling and other. The structural vibration consists mostly of race, click, squeal and cage noise: it can be continuous or intermittent depending on specific cases. The manufacturing vibration is instead related to the waviness noise generated by the geometrical imperfections of inner and outer ring and of rolling elements, being always continuous in nature. The so-called handling vibration is normally associated with flaw and contamination and is generating – in most of the cases – irregular noise. Then there are other types of vibrabition that include noise generated by sealing and lubricant (irregular) or by runout (continuous).
6.What is the load distribution within a ball bearing electric motor, and how does it vary between different bearing configurations?
The load distribution between the rolling elements and raceway is crucial in performance evaluation of rolling element bearings. Determine the load distribution by measuring the strain response at the bearing surface with a notched housing. Finite element analysis shows that the introduction of notches does not affect the load distribution. An experimental system was developed to investigate the load distribution in a cylindrical roller bearing. The experimental static load distribution agrees well with the theoretical calculation. The dynamic load at specific position of load zone reflects the manufacture difference among rollers and dynamic balance of distributing loads.
7.Do ball bearing electric motor come in various tolerance classes?
Bearing tolerances are standardized by classifying bearings into the following six classes (accuracy in tolerances becomes higher in the order described): 0, 6X, 6, 5, 4 and 2.
8.What is the production capacity of the factory for ball bearing electric motor?
The production capacity of Ningbo Haishu Nide International is:50000000pcs/month
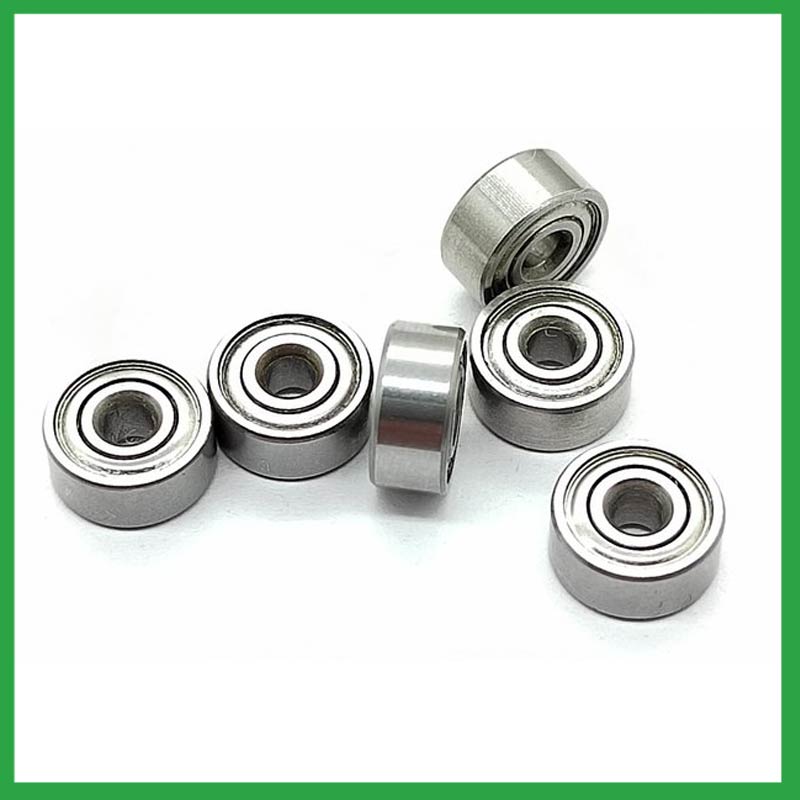
9.Are there specific ball bearing electric motor designed for applications in the aerospace and aviation industries, and what standards do they adhere to?
Airframe control ball bearing electric motor are specialized bearings tailored for aircraft structures, particularly control systems and surfaces. Designed for low-speed oscillatory applications, they offer precision and support, effectively managing misalignments and flight-induced stresses.
Airframe Control bearings are lightweight, corrosion-resistant, grease-lubricated, and are sealed on most occasions. They come in precision grades for running accuracy.
10.Can ball bearing electric motor be customized with special coatings or treatments to meet specific industry standards or regulatory requirements?
Yes, ball bearing electric motor can be customized with special coatings or treatments to meet specific industry standards or regulatory requirements.
1. Corrosion-resistant coatings: These coatings are used to protect the bearings from corrosion caused by exposure to moisture, chemicals, and other corrosive substances.
2. High-temperature coatings: These coatings are used to improve the thermal stability and performance of bearings in high-temperature environments.
3. Food-grade coatings: These coatings are specially designed for applications in the food and beverage industry, where bearings come into contact with food, beverage, or pharmaceutical products.
4. Anti-static and non-conductive coatings: These coatings are used to dissipate static electricity, which can cause damage to electronic components.
5. Specialized lubrication treatments: Bearings can be treated with specialized lubricants that meet specific industry standards or regulatory requirements.
11.How do manufacturers ensure the quality and reliability of ball bearing electric motor through material selection and precision machining?
High-precision measuring instruments, such as micrometers and gauges, are used to check the dimensions of the rings and balls to ensure they meet tight tolerances. Surface Finish Inspection: Surface finish is assessed using profilometers to ensure the required smoothness and low friction characteristics.
12.What are the considerations for selecting sealed or shielded ball bearing electric motor to protect against contamination and retain lubrication?
First, the environment in which your ball bearing electric motor operate in can help you identify potential contaminants, allowing you to select your shields or seals accordingly. For example, shielded bearings have a gap that can allow finer contaminants or water from washdown applications to enter the bearing and get into the raceways.The challenge for sealing bearings is to seal the bearing by protecting the bearing from contaminants and running efficiencies.
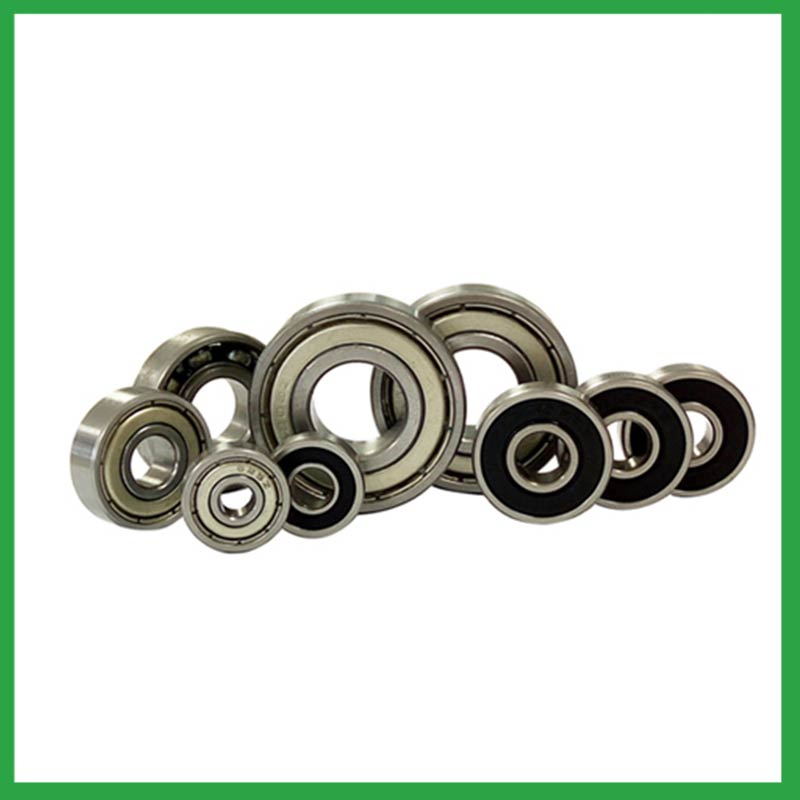
13.How do preloaded ball bearing electric motor enhance rigidity and reduce clearance in high-precision applications?
Enhance Rigidity: By applying a controlled axial force, preload increases the bearing's resistance to external forces and moments. This heightened rigidity is essential in applications where any deflection or misalignment must be minimized, such as in machine tools or robotic systems.
14.Are there self-aligning ball bearing electric motor that accommodate misalignment and shaft deflection in rotating equipment?
These ball bearing electric motor are particularly suitable for applications where misalignment can arise from errors in mounting or shaft deflection. A variety of designs are available with cylindrical and taper bores, with seals and adapter sleeves and extended inner rings.
15.How do different ball bearing electric motor designs, such as deep groove, angular contact, or thrust bearings, cater to specific applications?
Deep groove ball bearing electric motor: Deep groove ball bearings are the most common type. They can handle both radial and axial loads. Angular contact ball bearings: Angular contact ball bearings have higher than average internal axial clearance. They can handle axial loads in one direction and moderate radial loads.